Pneumatic lifting cylinders with air recycling
The added value of BORELLI group fillers
The pneumatic cylinders with air recycling were introduced on Borelli group fillers and monoblocks already in 2005. We have always asserted that the mechanical system in the lifting cylinder of the filler is not the most reliable solution from the technical point of view. For this reason pneumatic cylinders are mainly used on isobaric fillers and high performance fillers.
Since we were strongly convinced of this, in 2005 we started equipping our fillers, from the small semi-automatic rotary machine to the medium capacity equipments, with pneumatic cylinders abandoning the technology of the mechanical spring cylinder definitively.
Longer stroke and constant thrust. Fewer adjustments, more efficiency.
In detail the advantages of this solution.
In the pneumatic cylinder the thrust is constant on the whole stroke while in the spring cylinder the thrust decreases progressively while the piston and the spring extend. This system results in the maximum mechanical effort during the descent and the minimum thrust at the end of the stroke, exactly when it would be more important: during the opening of the valve.
The pneumatic cylinder maintains a constant thrust on the whole stroke and this leads to optimal pressure on the valve while working and slight resistance during the mechanical descent on the cam. In a few words: the working capacity improves and the wear and the breakage in the time are reduced.
Longer stroke and constant thrust. Fewer adjustments, more efficiency.
The pneumatic technology allows manufacturing, with the same overall dimensions, cylinders with much longer stroke if compared to the conventional mechanical cylinders. Normally a mechanical cylinder has a just sufficiently long stroke to lift the bottle till the opening point of the valve. This technical limit requires adjusting the height of the tank at any minimal variation of the height of the bottle.
The stroke of our cylinders is 150 mm, with constant pressure and therefore requires less frequent adjustments of the height of the tank. Referring to a level of 70 mm flush to the mouth it is possible to maintain the height of the tank unchanged for bottles with variations in height of 0/-40 mm. This is undoubtedly an advantage for all as to time-sparing and becomes indispensable for those who use returnable bottles and therefore have to work with glass containers with different heights.
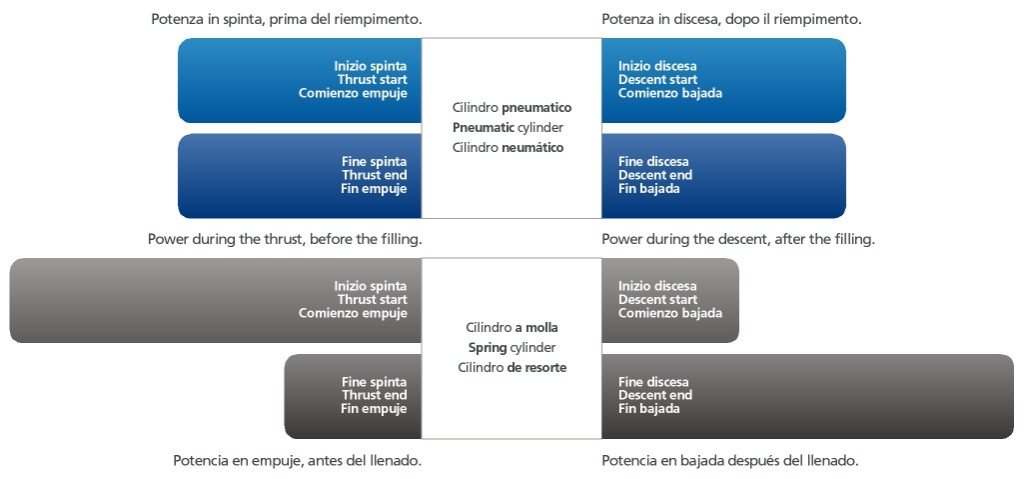
Easily adaptable thrust.
A further advantage is the possibility of varying the pressure of the cylinder simply regulating the inlet pressure of air in the circuit. In this way the thrust is easily adaptable to the type of valve fitted on the machine and the type of bottle processed. To vary the thrust of a mechanical spring cylinder the only way is substituting the spring, an unviable operation.
No wear.
Another remarkable advantage is the elimination of wear. As it is well-known springs degrade with work losing their original thrust. This means that frequent maintenance is needed to maintain the machine in full efficiency. The pneumatic cylinder does not wear and in the time it develops the same thrust regardless the number of hours worked.
The maintenance consists only in substituting the gaskets and only in the rare case of breakage. Moreover, said substitution is rapid and simple and does not require the intervention of specialized technicians. Our pneumatic cylinder is fully manufactured of stainless steel and slides on self-lubricating plastic material guides, therefore is not subject to oxidize. It can work even dry without any problems; however it is recommended to perform light lubrication.
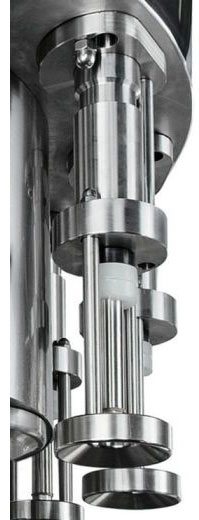
No thread in contact with the liquid.
For as good sanitization of the machine as possible from the technical point of view we succeeded in eliminating any thread in contact with the liquid. There is only a small welding made with TIG technology and perfectly polished. The wide passage surfaces and the extreme accuracy of the finish allow easy sanitization of the valve: difficult to imagine something better.
When in 2010 we introduced the EVO valve, we were convinced from the very beginning that our project was a break with the past: a new concept of filling valve with a brand new internal profile. The results of that work soon became evident in the fillers and monoblocks of BORELLI group that conquered ever more customers and new markets. Till today we have manufactured over 1,200 machines equipped with EVO valves. However we of BORELLI group do not content and our research still continues day after day. The remarkable number of machines produced every year allows us getting the proper feedback for the constant improvement of the product. We are not accustomed to underrating problems: a problem is a problem, even if it occurs only once, and deserves our attention to be solved. In this way, we can guarantee constant updating of the product thanks to the continuous interaction with our customers. Following this guideline the EVO valve could be improved in the years. Today, with eight years’ experience on over 1,200 machines equipped with the EVO valves, we propose the second series, EVO2, rich in new technological contents.
Adaptable to any filling system.
Gravity, low depression, high vacuum, or light pressure: the EVO2 valve performs its work perfectly adapting itself to all filling systems with perfect levels in the bottle without the aid of external levelling devices.
High standards of performance. The new internal profile, which is the result of a challenging and long work of design, enables attaining a high productivity of the filling valve. With this innovating valve the filling speed can reach throughputs of 1,600 litres/hour(1) with fillers equipped with 10 valves having an external section of 15 mm (standard valve for glass bottles). This performance can be obtained also through the gravity system, slower but more suitable for the bottling of wines and distillates, since it does not expose the liquid to flows of contaminated air and does not cause any dispersion of alcohol and flavours, inevitable side-effect of the depression system.
(1) The tests have been performed with water at ambient temperature and European Bordeaux bottles. The data are only indicative and can vary depending on the liquid used, the bottle and other external factors.
Self-levelling. The air return hole is located under the slider and therefore the valve is completely closed if there is no bottle. Besides the undisputable advantage of preventing any oxidizations of the filling liquid, this device guarantees perfect levels without using external levelling systems.
1) New rapid connection of the valve to the tank with bayonet system.Particularly useful in the cases when frequent substitutions of the valves are required to adapt the machine to special bottle formats such as miniature bottles. Besides, this solution facilitates the cleaning, the maintenance, and the sanitization of the valve.
2) New valve body with inside-out structure. This solution allows the complete discharge of the liquid during the washing.
3) Opening system for sterilization and drying. For pre- and post-bottling washing the valve is equipped with a forced opening system by means of a clip to fit to the rod. This very simple device enables an effective use of the steam during sterilization and is very useful in the stage after the bottling to maintain the valve open for perfect drying.
The system can be extended with the washing kit(2) consisting of auxiliary piping, stainless steel washing balls mounted inside the tank, special containers for the internal and external washing of the valve and liquid collection tray permanently located inside the chassis.
The whole system is designed for possible application of a CIP(3).
(1)Available to order. (2)Not supplied by BORELLI group
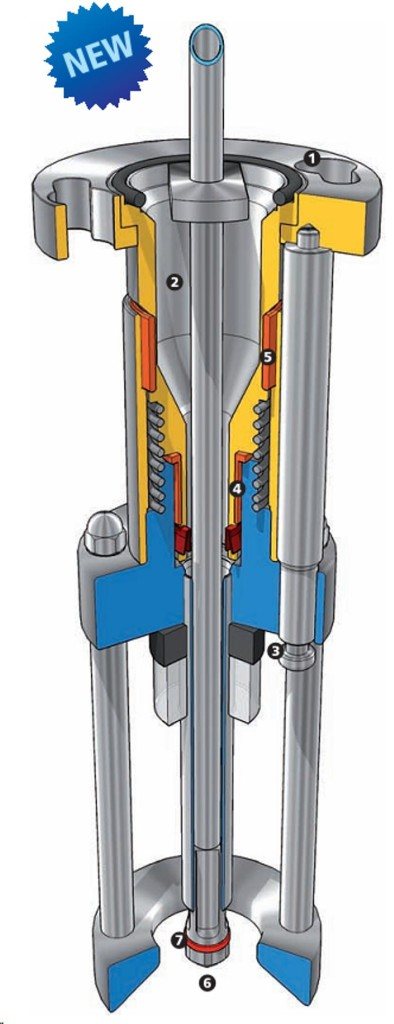
4) New profile of the valve body. The new design of the profile enabled us to insert a technopolymer bush between the body of the valve and the slider. With this device we gave an ultimate solution to the problem of possible grips, typical of the sliding of stainless steel on stainless steel. Besides, the particular position of this bush prevents any contact with the filling liquid even in case of breakage of the internal gasket.
5) External guide on self-lubricating bush.We also introduced a guide outside the body working on a self-lubricating bush. This device, apparently unnecessary, allowed us maintaining greater mechanical tolerance in the internal guide, the one between the body of the valve and the slider, with the advantage of higher resistance to wear and better mechanics of the whole valve.
6) New profile of the point. The refashioned technical drawing maximizes the passage of the liquid while the de-aeration tube enlarged to 8 mm ensures optimal performances even with particularly foaming wines or liquids.
7) New gasket on the point of the valve. The new gasket improves the descent of the liquid on the wall of the bottle and consequently the evacuation of the air outwards, so remarkably increasing the performance of the valve. Besides, it has a better profile and more solidity to guarantee long life even under critical working conditions, like with the use of steam or acids for the sterilization or in the case of hot bottling.
FUTURA V2.0, tradition and technology.
FUTURA V2.0 is the conventional capper for alumium screw caps with speed rates up to 3,000 bph and represents the final evolution of this type of machines. We think it will be hard to introduce further improvements. The framework supporting the turret is an extremely sturdy central column of stainless steel hosting the manual, or optionally electrical, lifting system.
Its exceptional sturdiness is visible at first sight.
1) The caps chute, completely assembled with laser-cut stainless steel profiles, shows precision and sturdiness unknown till today.
2)The photocell on the chute controls both the start of the feeder and the machine stop in case of lack of caps automatically.
3)The 4-roller closing head is manufactured completely of stainless steel and is equipped with the NO CAP, NO ROLL device preventing the spinning in case of bottles accidentally arriving without the caps so protecting the glass container and the integrity.
ALEXA V2.0, simple technology
If you need to close your bottles with aluminium screw caps, today you can choose also the new capper ALEXA V2.0, an extraordinary combination of simplicity and technology. The high level of its technological features is evident at first sight.
1) The caps chute, completely assembled with laser-cut stainless steel profiles, shows precision and sturdiness unknown till today.
2) The photocell on the chute controls both the start of the feeder and the machine stop in case of lack of caps automatically.
STELVIN® caps
Among the alternative closures for wine put on the market in the recent years, the STELVIN® caps have con-quered an important share.
We at BORELLI group believed in the potential of this closure since the very first moment and therefore we developed specific solutions for this caps, with special attention to the size 30×60, very popular all over the world.
Besides being equipped with all technical solutions found with the experience acquired in the closure of these caps, also the turret ALEXA V2.0 has the simplicity characterizing all BORELLI group solutions. As always, the result is even better than the expectations of the most demanding customers: an economical and simple, yet extraordinarily functional and sturdy machine.